Standard or standardized work instructions (SWI) are instructions, specifically designed to ensure the consistency, timing, and repetition of the processes. You’ll recognize them as printed papers, put on tables or boards next to the operator’s work stations. Standard work instructions are subject to lean manufacturing’s approach of continuous improvement, also called Kaizen. It refers to documentation and the following of best manufacturing practices with constant improvements and updates. In short, update your standard work instructions with new ways of doing things regularly and eliminate any possible waste that adds extra time or lowers the quality of your products.
Without standard work instructions, operators would have to rely on collective memory to perform the tasks. This toughens the process as we all know how different people can remember things differently. To improve the effectiveness, it is crucial to have clear standard work instructions, understandable to both, operators and managers. This is what the word standardized stands for; the ability to be followed by everyone.
If using standard work instructions, your work will show 4 improvements in:
- The quality of the finished product
- The consistency of the finished product
- Throughput of the process
- The operators’ safety
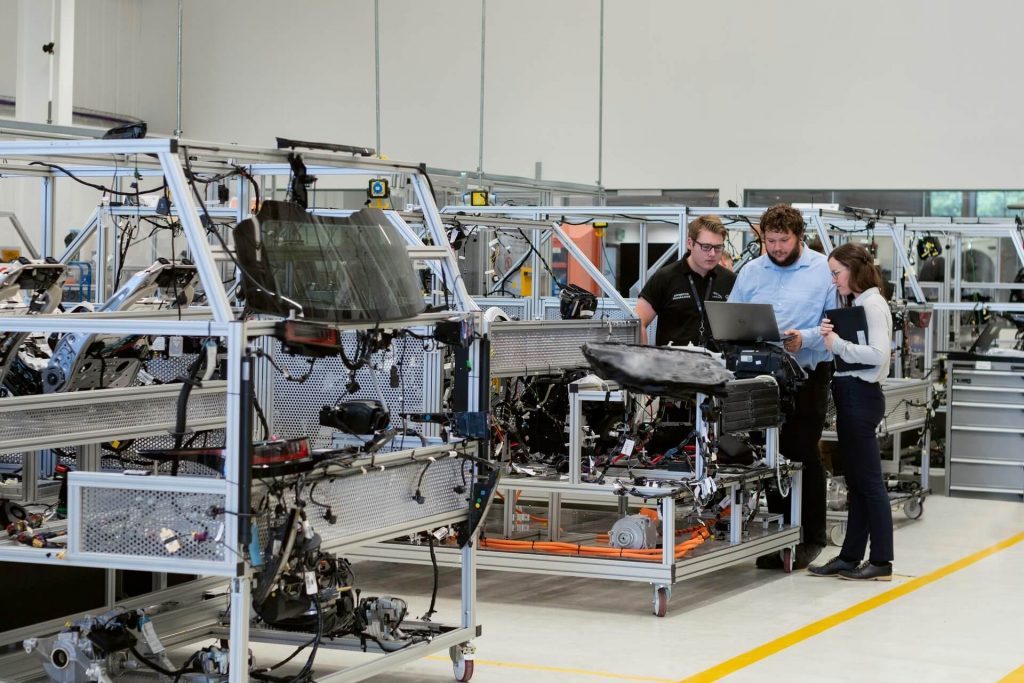
Write standardized work instructions for lean manufacturing in 5 easy steps
If you wish to succeed in your lean manufacturing documentation, consider 3 questions before writing it: who performs the task? When do they perform the task? And how do they perform it? Answers will provide you with inputs for further design of lean standardized work instructions.
Do you already have the answers to the questions in mind? Great. Now follow the 5 steps to create standardized work instructions in lean manufacturing:
1. Observe work
Start with an observation of a task you wish to standardize. You can design a process study sheet in Excel and print it to help you with notes. When collecting details, be sure to use correct real times, stay focused and don’t guess what the workers are doing.
2. Understand the throughput of the process
Understand cycle times, inputs and outputs and the capabilities of how many parts per period can be delivered, so understand the throughput. Focus on takt time and line balancing. You can do some simple calculations for the two, provided you have the information on the length and number of products produced in a process.
3. Define the task steps
By using a standard work chart document, define the exact sequence of the steps, needed to perform a certain task. You can add images, charts and tables to visualize it. Also, don’t forget to include the information on whether the process succeeded or failed.
4. Document the standard in-process inventory
Keep in mind that lean manufacturing’s goal is to minimize it. Think about the requirements for the inventory at the beginning and end of the process and how much stock will the semi-products create in between the steps.
5. Create a combination table
Join the steps and create a comprehensive image of the process. The most common combination table is a Gantt chart. It allows you to see how much time does each step take, who is responsible for it and which steps need to be completed to move on to the next ones. This is usually done by the project office and includes real-time dates of the tasks. SWI tasks following the lean manufacturing Kaizen approach need to be updated regularly, to ensure the best quality and consistency. Designing standardized work instructions in lean manufacturing by following the 5 steps will result in the work will be done faster, problems solved quicker, waste reduced and costs lowered.